


Ninso
Project
We are excited to highlight that this project is among our pioneering ventures, showcasing our commitment to delivering exceptional solutions. Let’s explore in detail the impressive outcomes we achieved for Ninso through this project, demonstrating our expertise in driving efficiency and profitability for our clients.
Background
Ninso, renowned for its RM2.40 products, faces higher delivery costs relative to the product price. To address this challenge, it is essential to prioritize cost-effectiveness in warehouse management systems and maximize return on investment (ROI).
Challenges Faced
-
The international warehouse management system failed to align with Ninso's unique workflows and processes.
-
Disorganized procedures lacking standard operating procedures (SOPs).
-
Excessive workforce within the warehouse, leading to inefficiencies.
-
High levels of manual labor contributing to operational delays.
Strategic Solutions and Results
Recognizing these challenges, we implemented tailored strategies focused on optimal resource utilization and financial benefits:
-
Consolidated warehouses for greater efficiency.
-
Transitioned to full customisation SEATT Warehouse Management System (WMS) for enhanced functionality.
-
Embraced digitalization within the warehouse operations.
-
Reduced workforce to streamline operations.
-
Achieved more than a 3x increase in efficiency.
By focusing on these solutions, Ninso improved its warehouse management and enhanced its overall operational effectiveness.
#1 Consolidation of Warehouse
Initially, Ninso operated five warehouses in Klang Machap, but high overhead costs and disorganized inventory posed significant challenges. Therefore we provided the strategy of relocation of warehouse and combined five warehouses to one bigger warehouse





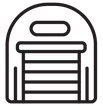
#2 Change of Warehouse Management System
Most international branded warehouse management systems (WMS) are challenging to customize for the specific processes and cost-effectiveness needs of various clients and industries. As a result, clients often must alter their operational advantages to accommodate these systems. In contrast, the SEATT warehouse management system offers full customization, including assistance in setting up standard operating procedures (SOPs). This flexibility enables improved warehouse efficiency and effectively supports clients in their critical operational areas.
#3 Digitalisation of Warehouse processes
With the implementation of the SEATT warehouse management system and standard operating procedures (SOPs), the system is seamlessly integrated into various processes such as receiving, in-bin management, cross-docking, picking, replenishing, daily cycle counts, stock takes, and outbound operations. This integration allows the system to monitor all warehouse operations, automatically triggering alerts and providing instructions for workers to perform their tasks. As a result, warehouse employees can simply follow the prompts on their tablets, enabling them to execute their jobs accurately and efficiently, minimizing the risk of errors.








#4 Reduced Workforce
After the implementation of the SEATT warehouse management system, workforce efficiency significantly improved over the course of one year, leading to a reduction in manpower from 250 employees to just 150 within the warehouse.
250
150
#5 3 x efficiency increase!!
Since the implementation began in 2020, Ninso's warehouse has experienced a daily outbound efficiency increase of over three times its original volume, even as the workforce was reduced from 250 to 150 employees. Remarkably, the same warehouse with the reduced workforce now services more than 60 outlets, up from just over 30. This transformation has led to a decrease in warehouse costs and an increase in overall revenue.